Контрол на качеството на пътните настилки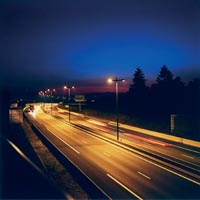 Контролът на качеството е от първостепенна важност при всички строителни и производствени дейности. За жалост, при съвременните темпове на строителство, този етап много често се пренебрегва. А не бива да се забравя, че дори при отлична проектантска дейност е възможно неправилното изпълнение и лошо подбраните материали да компрометират всеки строителен проект
текст инж. Вера Ангелова Реално погледнато, пътните настилки са една от сравнително лесните за изпълнение строителни работи, особено при наличието на съвременната, мощна асфалтополагаща техника. Затова е странно, защо те често се развалят броени дни, след като са изпълнени. На практика състоянието на цялата национална пътна мрежа може да се опише като плачевно. Дори опитите за поправяне не винаги се оказват удачни, а един блокиран поради ремонтни дейности път нарушава нормалния ритъм на автомобилния трафик и причинява много излишни нерви. Освен това, не бива да се пренебрегват и разходите, които са неизбежни при реконструкция на пътища и никак не са малки.
Но когато качеството е гарантирано още на етап изпълнение, всички тези проблеми могат да бъдат избегнати.
Зачестилите напоследък инциденти с новоизпълнени пътни настилки доказват належащата нужда от професионален контрол на качеството. За такъв контрол са необходими модерна техника и добре запознати с работата с нея кадри.
За определяне на повечето необходими физични и механични параметри на асфалтобетонните настилки са възможни два подхода - лабораторно или безразрушително изпитване (in situ). При първия вариант се изрязват ядки от асфалтовия пласт, които се подлагат на различно натоварване, в зависимост от търсената механична характеристика. При безразрушителното тестване целостта на настилката се запазва, а търсените параметри се определят индиректно, като функция на лесен за измерване показател, като повърхностната твърдост, например. По правило лабораторните изпитвания дават по-голяма точност на резултатите, но за по-отговорни проекти е препоръчително комбинирано използване на двата метода, защото безразрушително тестване може да се осъществи по цялата дължина на настилката, докато при лабораторното изпитване не е сигурно дали извадената ядка е със същите показатели както останалия асфалтобетон.
Качества на асфалтовата смес
Традиционно изпитване за намиране на якостните характеристики на горещата асфалтобетонна смес е методът Маршал. Но в последните години все по-убедително се доказва, че получените чрез него резултати не са особено надеждни. Както в много други области на науката и техниката, разработените напоследък методи и технологии осигуряват много по-висока точност и сигурност, защото отчитат много повече фактори, чието влияние е било пренебрегвано преди.
Такъв модерен метод за изпитване на асфалтобетон е използването на т.нар. въртящ се уплътнител. Той е идеален за симулиране на поведението на положените настилки във времето. Допълнителното уплътняване, дължащо се на движение на автомобили в дългосрочен период, може да бъде пресъздадено със значителна точност, благодарение на комбинираното действие на статичен натиск и срязващи сили. Освен това, температурата на провеждане на изпитването съвпада с реалната експлоатационна температура, което е още една гаранция за надеждност на резултатите.
Въртящият се уплътнител представлява стандартно цилиндрично тяло с нормиран диаметър. В него постъпва почвената проба, статичното и динамичното натоварване се създава от пневматична система, а резултатите се обработват от автоматична система за регистриране и обработка.
Въртящият се уплътнител може да се прилага при различни видове смеси - рециклиран, порьозен бетон - дори е разработен във форма, приложима за студени смеси.
Чрез него се определя съдържането на въздушни пори в сместа за всеки един етап от изследването и при даден брой обороти. Той позволява и да се създаде зависимост на плътността от броя на оборотите. Но най-голямото му предимство са компактните размери, които позволяват провеждане на тестове на място, по време на полагане на настилките.
Европейските норми препоръчват нова и по-точна методика от традиционния метод Маршал и при определяне на коравината и устойчивостта на умора и остатъчни деформации.
Според EN 12697-26, анекс В, коравината трябва да се определя чрез четириточково изпитване на огъване на призматични асфалтови пробни тела, които могат да са изрязани от пътни настилки или да се подготвят в лабораторни условия.
За получаване на по-пълна картина на якостните показатели се прави и индиректно изпитване на опън, което се провежда с цилиндрични пробни тела с различни диаметри.
При четириточковото изпитване на опън, призматичното тяло се фиксира и в четири точки, разположени симетрично, се прилагат периодично сили със синусоидално изменение, предизвикващи огъващи моменти. Натоварването се осъществява чрез вертикално отместване на четирите точки, перпендикулярно на надлъжната ос на пробното тяло. По време на изпитването силата, предизвикваща огъващ момент се измерва като функция на времето, а също и изоставането по фаза между сигнала на силата и този на деформацията. С помощта на тези данни се изчислява модулът на коравина.
Необходимата апаратура за това изпитване се състои от солидна метална рамка, чрез която се осъществява фиксиране на призматичния елемент и подаване на натоварването. Във всеки момент на тестването регистрираща система записва стойността на огъващия товар и хоризонталните деформации. Уредът за изпитване на индиректен опън има подобна конструкция, но е значително по-опростен и компактен, защото предава натоварването само чрез една повърхност. За целта се използват вдлъбнати планки от неръждаема стомана. Тяхната заобленост се определя от диаметъра на асфалтовата ядка.
Товарещият механизъм прилага пулсиращо натоварване с периоди на почивка по вертикалния диаметър на цилиндъра. Записващата система отново регистрира стойностите на приложената сила и хоризонталните деформации.
Устойчивостта на умора е друга базова характеристика, от която зависи дълготрайността на настилката. Умора на материала настъпва вследствие на многократно повтарящо се във времето и често различно по посока динамично натоварване. Вследствие на нея якостите на асфалтобетона при последвало натоварване са значително занижени и е възможно компрометиране на инженерното съоръжение. За определяне на конкретната устойчивост на умора за дадена настилка и при оптимизирането на горещите смеси по отношение на динамичната устойчивост, се използват същите уреди, с които се изчислява коравината. Натоварването, предизвикващо умора, се симулира от уреда за четириточково огъване, като за определяне на устойчивостта отново се използват призматични пробни тела (гредички). Създават се огъващи моменти в средните точки на гредата чрез вертикалното им преместване, докато крайните опори остават неподвижни във вертикална посока. Големината на натоварването се изменя синусоидално. За да се постигне достоверна стойност на устойчивостта на умора, се правят голям брой изпитвания при различни честоти. Затова системата за натоварване трябва да позволява използване на честоти от 0 до 60 Hz, като капацитетът на натоварване е препоръчително да е около 2kN с клас на точност 0.2.
Съществува и алтернативен метод за определяне на устойчивостта на умора - чрез изпитване на индиректен опън. Използва се типичното за такова изпитване цилиндрично пробно тяло. Върху него се прилага многократно натоварване на натиск, изменящо се по аркуссиносова крива във времето и действащо върху вертикална диаметрална равнина. При последния цикъл на натоварване (когато се изчерпва устойчивостта на умора), изпитваният цилиндър се разцепва вертикално през оста на симетрия. Резултатите, които се отчитат и обработват при това изпитване, са хоризонталната деформация (в mm) и броя на приложените цикли на натоварване. Зависимостта на преместването от броя цикли може да се изрази и графично чрез възходяща крива.
Контрол на положения асфалтов пласт
Един от най-важните показатели, чиято стойност трябва да се определи със значителна точност за всяка асфалтова настилка, е коефициентът на уплътнение. Неговата стойност показва доколко може да се разчита на проектната стойност на якостните показатели. Ако обемът на порите се окаже по-голям от предвиденото в проекта, якостите ще са значително по-малки от очакваните.
Процедурата за определяне на коефициента на уплътнение се базира на сравняване на обемните плътности на ядки, изрязани от пласта положена смес, и предварително изготвени пробни тела. Алтернативен метод за изчисляване на плътността е безразрушителното тестване. При него резултатите се получават значително по-бързо и в повечето случаи точността е добра.
Други параметри на асфалтовите настилки, които трябва да се следят и контролират при полагане, са равността, дебелината на настилката и напречния наклон. За определяне доколко положеният пласт е равен, се използват подвижни триметрови лати, снабдени със записващо устройство. Възможно е и използване на четириметрови лати или автоматичен уред APL, в зависимост от изискванията на проекта. Дебелината и наклонът се измерват чрез подходящи геодезически уреди. Допускат се само минимални отклонения от проектните стойности. При контрола на положения асфалт трябва да се обърне внимание и на текстурата на готовото покритие, както и на сцеплението между два пласта, лежащи един над друг.
При асфалтиране трябва да се спазват и някои универсални правила. Полагането на асфалтобетона не бива да става при температура, по-ниска от 7°С и в никакъв случай - върху замръзнала основа. Това би означавало пропадане на настилката още първата пролет, при повишаването на температурите. Основата също трябва да е одобрена и приета като якост и дебелина. Специално внимание се обръща и на хоризонталните и вертикалните работни фуги. Те трябва да се разминават по дебелина на настилката и да са обработени за осигуряване на добро сцепление.
Разбира се, преди да се стигне до полагането, асфалтовата смес изминава дълъг път. Контролът на качеството е задължителен на всеки етап от производството й. Като начало е необходимо да се проверят качествата на вложените материали. Фракциите едър и дребен добавъчен материал трябва да съответстват на нормативните и проектните изисквания. За чакъла се прави и оценка на формата на зърната. Наличието на пръчковидни и плочковидни зърна се ограничава, за да се гарантира изотропност на сместа. Трябва също да се провери доколко сцеплението със свързващото вещество е добро и дали мразоустойчивостта е достатъчна при конкретните климатични условия.
За пясъка се препоръчва пресяване с миене, за да се ограничи наличието на прах, глина и органични частици и да се постигне желаният зърнометричен състав. Минералното брашно също трябва да отговаря на нормативната зърнометрия.
За битума се определят пенетрация, дуктилност и температура на омекване. При производството на сместа се контролират точността на дозиране на материалите, температурите на загряване на отделните компоненти и времето за смесване.
За никого не е тайна, че националната ни пътна мрежа е под всякаква критика. Също така се знае, че това е област от икономиката, в която се очаква да постъпят много инвестиции в идващите години. Затова е важно пътните настилки да се проектират и полагат с професионализъм, без да се пренебрегва контролът на качеството на нито един етап. Средствата, вложени в тестваща апаратура, се възвръщат многократно чрез спестените пари от ремонти.13/09/2007 |