Градски водопроводи за питейна вода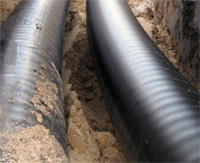 Във водоснабдяването на населени места през последните десетилетия все повече се използват различни пластмасови тръби. Използването на такива тръби позволява да се пести метал, да се намалява продължителността на монтаж на водопроводите, както и удължаване на техния експлоатационен срок - 50 и 100 години. Това обстоятелство се дължи на факта, че пластмасовите тръби не са подложени на корозия, като гладката им повърхност осигурява по-голям мрежов капацитет със същия диаметър.
В статията ще разкажем за полиетиленовите тръби с черен цвят и сини линии - HDPE/PE100, за съединяването и траншейното полагане на полиетиленовите тръби - PE100, за центрофугално лятите напорни стъклопластови тръби - GRP-CC, за съединяването и полагането на стъклопластовите тръби - GRP-CC.
Пластмасите, поради сравнително ниската си цена, гъвкавост и устойчивост към водата, се използват за производство на тръби, предназначени за пренос на питейна вода. Те заместват много широко разпространените продукти във водоснабдителните мрежи, такива като цимент и метали. Обикновено пластмасата се предпочита пред метала, поради редица нейни предимства. Пластмасовата тръба е лека и не е нужен открит огън за свързването им. Гъвкавостта на пластмасата улеснява монтирането є. Сред многото пластмасови тръби най-голям интерес за външни водопроводи представляват полиетиленовите с различна плътност - РЕ, и стъклопластовите - Glass-reinforced thermosetting plastics “GRP” based on unsaturated polyester resin “UP”- Усилени със стъклени влакна термореактивни пластмаси “GRP” на основата на ненаситени полиестерни смоли “UP”. Стъклопластът е композитен материал, състоящ се най-малко от два различни материала - полиестерна смола, армирани стъклени влакна, и пясък като пълнител. Обединяването на материалите позволява съчетаване на техните предимства в един общ краен продукт. Най-често стъклопластовите тръби се класифицират по номинална коравина в N/m²-SN, по максимално работно налягане на водата в MPa при 20°C за 50 годишен експлоатационен срок на тръбата-PN, по номинален диаметър на тръбата в класове с налягане-DN. Напорните тръби от полиетилен са изработени с „high density”-HDPE - висока, „middle density”- MDPE - средна, и „low density”- LDPE ниска плътност. Нивото на плътността, изразява налягането, на което тръбите могат да издържат. За външни водопроводи с трайно високо налягане или натоварвания, като улиците, се използват HDPE тръби. Според „Наредба № 2 от 22 март 2005 г. за проектиране, изграждане и експлоатация на водоснабдителни системи, минималният диаметър на тръбите на водопроводната мрежа в урбанизирани територии с население над 100 000 жители е 100mm, а за територии с население под 100 000 жители-80 mm. Максималният допустим хидростатичен напор във водопроводната мрежа на населените места е 0,6 МРа.
Полиетиленови тръби с черен цвят и сини линии HDPE/PE100
HDPE/PE100 е материалът използван в производството на напорни водопроводни тръби за изграждане на външни мрежи и сградни отклонения за питейно-битово водоснабдяване. Числата в абревиатурата PE100, разделени на 10, показват „minimum required strength”-MRS - минималната изисквана якост на материала в MPa, а именно, 10.0MPa. Минималната изисквана якост на полиетилена показва какви са вътрешните напражения, които тръбата трябва да издържи, без да се разруши вследствие на налягането на водата в нея. Увеличаването на MRS на полиетилена позволява да се произвеждат тръби с по-тънки стени, което на свой ред увеличава светлото сечение на тръбите и подобрява хидравличната им проводимост, както и якостта им при по-високи налягания. Сега най-актуалният и използван материал за производство на напорни полиетиленови тръби е PE100. Експлоатационният опит е показал, че, освен якостта на полиетилена на налягането на водата в тръбите, от особено значение е и якостта му на бавно образуване на пукнатини. Причината е образуване на шупли по повърхността от одрасквания и натоварване от по-едри и остри предмети в обратната засипка на тръбата. Образуването на драскотини при полагане на тръбите и нарастването им с времето до пукнатини намаляват работното сечение на стената на тръбата, което води до увеличаване на вътрешните напрежения в материала. В тези зони с увеличено напрежение най-често възниква пробив в структурата на тръбата и оттам авария със загуба на вода. Това е накарало производителите на пластмасови тръби да положат допълнителен защитен слой от полипропилен или пенообразен полиетилен. В днешни дни най-популярно е производството на полиетиленови тръби - PE100, които са устойчиви на пукнатини - resistant to crack - RC, т.е. PE100RC.
Тръбите от PE100RC, подобно на тръбите от PE100, могат да бъдат с или без допълнителен защитен слой. Новият клас на напорни полиетиленови тръби - PE100RC, на практика е PE 100 с добавена повишена устойчивост срещу бавно нарастване на пукнатини по повърхността на тръбата. Следователно PE100 и PE100RC като начини на свързване, полагане, хидравлична проводимост и статическа устойчивост, са идентични. Тръбите PE100RC гарантират по-малка вероятност за образуване на пукнатини. Ако се е образувала пукнатина по повърхността на тръбата, тя ще нараства много по-бавно при равни други условия, в сравнение с тръбата PE100.
На пазара, според Publicly Available Specification-PAS 1075 - Германия, се предлагат следните видове напорни полиетиленови тръби със защита срещу бавно нарастване на пукнатини. Еднослойни плътностенни тръби от PE100RC, съгласно DIN8074/ISO4065. Двуслойни тръби от PE100, с допълнително екструдиран в размера вътрешен защитен слой-RC. Трислойни тръби от PE100, с допълнително екструдиран в размера вътрешен и външен защитен слой от RC. Тръби с размери по DIN8074 с външно повърхностно добавено защитно покритие.
Еднослойните компактни тръби изцяло произведени от PE 100RC показват изключително голяма устойчивост срещу бавно развиване на пукнатини и голямо точково натоварване на външната повърхност. Това в голяма степен определя по-дълъг експлоатационен живот - 100 години, в сравнение с тръби произведени само от PE100 или т. нар. многослойни ко-екструдирани тръби. При последните, най-често външната повърхност е от PE100RC, а останалата част е от PE100. Ако първоначалната драскотина е прорязала, целият PE100RC-слой, и е достигнала до PE100-слоя, тогава нарастването на пукнатината ще се ускори и многослойната тръба ще бъде много по-уязвима от еднослойната компактна тръба.
Тръбите с размери по DIN8074 са направени от основна тръба от PE100RC и външно защитно покритие - например полипропилен - РР. Допълнителното защитно PР-покритие, дава допълнителна сигурност срещу образуване на шупли, а оттам и на пукнатини при складиране, транспорт, разтоварване и полагане. Минималната дебелина на защитното покритие възлиза на 0,8 mm. То зависи от диаметъра на тръбата. При по-големите диаметри, дебелината му е по-голяма поради по-големите натоварвания. Якостта на свързване между основната тръба и защитното покритие трябва да е толкова голяма, че при полагането да издържа на възникналите вътрешни сили на приплъзване. Тръбите са с възможност за интегрирана детекторна жица. Вградената детекторна жица спестява време за прокарването на допълнителна детекторна лента над тръбата. Поставянето на последната е възможно само при траншейно полагане с обратна засипка. При безтраншейно полагане, водопроводът няма да има детекторна лента и по-трудно ще може да се локализира. Тръбите с размери по DIN8074 с външно защитно покритие, са идеално решение за бързо и лесно полагане, без пясъчно легло и без изкоп.
Разликата в цените на изходната суровина за PE100 и за PE100RC е все по-малка в сравнение с допълнителната сигурност, която PE100RC имат срещу нарастването на пукнатини. Това до голяма степен обезсмисля икономисването за сметка на сигурността, което се получава при многослойните тръби от PE100 и PE100RC. По-доброто и сигурно решение, са еднослойните компактни тръби от PE100RC.
Съгласно производствения стандарт БДС EN 12201-1, гранулатът, от който се произвеждат полиетиленовите водопроводни тръби, трябва да е предварително оцветен, в цвета на крайното изделие. Ако тръбите трябва да са черни, гранулатът е черен, ако трябва да са сини, гранулатът е син и т.н. Стандарт БДС EN 12201-1 забранява използването на безцветен PE-гранулат, при производството на полиетиленови водопроводни тръби. Причината е, че само предварително оцветеният гранулат гарантира хомогенна структура на произведените тръби, добра дългосрочна устойчивост на налягане и добра еластичност на материала. При използване на безцветен полиетилен и последващото му оцветяване по време на производството, води до получаване лошо хомогенизиране на материала и влошаване на качеството на тръбата-намаляване на експлоатационния срок, възможно спукване на тръбата. Такива тръби не могат да издържат лабораторните тестове за вътрешно хидростатично налягане и опън. Следователно, напорните водопроводни тръби PE100, тябва да са произведени от предварително оцветен HDPE по ISO 9001 или еквивалент, от водещи фирми на международния пазар. Произвежданите в България еднослойни плътностенни тръби - PE100RC, по БДС EN 12201-2 и DIN 8074, с DN16-1200 mm и PN6-32 bar, са черни на цвят с надлъжни сини ивици с дължини 6-12 m. Предназначени са за прави участъци при изграждането на магистрали за студена вода в населените места. Индикатор за съпротивлението на тръбите е Standard Dimension Ratiо-SDR-стандартен коефициент на размера. Тази уникална характеристика показва съотношението на номиналния външен диаметър тръбата към номиналната дебелина на стената є. Тя е част от маркировката на полиетиленови тръби. Диапазонът на величината е от 6 до 41. Най-високите стойности са характерни за тръбни продукти с тънки стени. Тръбите с дебели стени винаги имат малък SDR, т.е. те са по-устойчивите напорни тръби. Експлоатационният им срок зависи от такива фактори, като вътрешно налягане и външни натоварвания, например когато тръбопроводът е покрит със земна маса. Всеки тръбен продукт отговаря на определени показатели за налягане. Според тези характеристики се определя предназначението на тръбата в инфраструктурните системи. Възможните приложения на произвежданите в България PE100RC е следното. 6BAR(SDR 26) - за снабдяване с питейна вода на населени места с малка площ. 10 BAR(SDR 17) и 16 BAR(SDR 11) - за полагане на магистрални тръби в населените места с ниско налягане на питейна вода. 20 BAR(SDR 9) и 25BAR(SDR 7,4) - подходящи за снабдяване с питейна вода под високо налягане.
Съединяване на полиетиленови тръби PE100
За присъединяване на полиетиленови тръби е възможно използването на различни методи на свързване - заваряване със струя топъл въздух, с преносим екструдер, челно заваряване с термопластина пластина, заваряване чрез стопяване. При изграждане на водопроводни системи се използват предимно методите на челно заваряване и заваряване чрез стопяване.
Заваряването е процес на термично сплавяване с нагряване до 220°С. Кръговите отвори на съединяваните полиетиленови тръби се нагряват до постигане на състояние на разтопеност на всяка контактна повърхност. След това двете повърхности се съединяват под контролиран натиск за определен период на охлаждане. Молекулите на двете тръби се съединяват и се получава хомогенна заварка.
Челната заварка чрез термично сплавяване е напълно приложима, при заварка между две тръби от PE100RC, между една тръба от PE100 и PE100RC, и между две тръби от PE100RC с допълнителен защитен слой от РР.
При челното заваряване се използва специална заваръчна машина с нагряваща плоча - „огледало“, за нагряване на краищата на тръбата до точката на топене. След постигнатото разтопяване краищата на тръбите се съединяват под налягане. Заваръчната процедура протича в следната последователност. Заглаждане на краищата на тръбите в заваръчната машина с подравняващо устройство и проверка за съосие. Притискане на краищата на тръбите към термоелемента с необходимото изравнително налягане до момента, в който се образува ивица от разтопен материал с височина 2 mm. Намаляване на изравнтелното налягане до нула, и нагряване без натиск, до разтопяване на необходимата полиетиленова маса около заваряваната площ. Освобождаване на краищата на тръбите от нагряващия елемент-огледало, след определеното време и незабавно съединяване на тръбите при заваръчно налягане, поддържано през целия период на охлаждане до завръщане на материала в твърдо състояние. Заварката не трябва да се размества‚ докато зоната на шева не се охлади естествено до температура около 60°С. Времето на охлаждане, налягането за нагряване и заваряване, височината на образуваната заваръчна ивица, зависят от диаметъра и дебелината на стената на заваряваните тръби.
При заваряване чрез стопяване се изисква специален агрегат за контролиране на заваряването, който изпраща топлинна енергия - прав ток, към специалния полиетиленов фитинг за стопяване. Фитингът представлява съединяващо приспособление с две гнезда с нагряващ елемент-реотан, оформен по повърхността за заваряване при точките на свързване, т.е. той е електромуфа. Когато двата подравнени края на тръбата се въведат в приспособлението и се подаде ток, топлината, генерирана в елемента, споява присъединяваните повърхности. Времето за спояване и подаването на ток, които зависят от диаметъра и типа на фитинга, се регулират ръчно или автоматично от контролно табло. И тук от голяма важност е доброто почистване на контактните повърхности на тръбите.
Механичното съединяване на полиетиленовите тръби се осъществява чрез механични фитинги-пластмасови или метални. Използват се фитинги за многократно ползване или трайно монтирани. Фитингите трябва да отговарят на физико-химическите характеристики на тръбите. Такива фитинги могат да се произвеждат чрез леене под налягане или в случай‚ че не се намират на пазара‚ те се получават директно от тръбата чрез челно заваряване на сегменти-огъване‚ челна заварка с вставяне на материал и т.н.
Траншейно полагане на полиетиленови тръби PE100
При траншейното полагане на полиетиленовите тръби с висока плътност в градски условия, механизирано се прави изкоп с дълбочина – 1,50 m. По принцип размерите на каналите се определят според диаметъра на тръбите, метода на свързване и типа на почвата. Ширината на изкопа не може да е по-малка от диаметъра на тръбата плюс 60cm за тръби с диаметър по-макък от 500 mm и 1 m за тръби с диаметър по-голям от 500 mm. Преди полагането на тръбите се проверяват дълбочината на полагане, откосите, широчината и състоянието на дъното на изкопа. Дъното на изкопа трябва да бъде равномерно и без камъни и други остри и твърди предмети. Необходимо е то да бъде покрито със слой от пясък с дълбочина 15-20 cm. Този слой осигурява равномерна опора на положената полиетиленова тръба. Следва спускане и полагане на полиетиленовата тръба в изкопа и направа на връзките. Ако не съдържа камъни, изкопаната пръст може да бъде използвана като страничен материал и за запълване. Тръбата, странично и поне на 20 cm над нея се засипва с пясък или мека почва, а след това със земна маса на пластове с дебелина 20-30 cm. Пластовете с трамбоват. Целта е правилно утъпкване и разпределение на натоварването на земната маса върху тръбата.
Центрофугално ляти напорни стъклопластови тръби GRP-CC
GRP pipes produced by centrifugal сasting (CC) - тръбите от центрофугално лят стъклопласт се произвеждат от термореактивни пластмаси - ненаситена полиестерна или винилестерна смола, нарязани стъклени влакна и подсилващи агенти. Стандартната структура на тръбната стена е такава, че всеки от отделните материали, допринася със собствените си свойства за тези на крайния композит. Смолата прониква във всички компоненти и създава здрава връзка между тях. В зависимост от изискваните параметри на тръбата, като коравина-деформационна якост, клас на налягане и химическа устойчивост, се използва определен метод, за изработване на стандартизирана структура на стената. Стената на тръбата се изгражда постепенно отвън навътре във въртяща се матрица с увеличаване на скоростта, след като всички суровини са в нея. Високата центробежна сила притиска материалите към стената на матрицата. Останалият въздух се извежда и суровините се сгъстяват до максимум, като се създава висококачествена плътна структура на стената. Шупли не се образуват. Колкото по-голяма е дебелината на стената, толкова по-висок е класът на коравината й. Той определя способността на стената да издържа на огъващи външни натоварвания или ниско вътрешно налягане. Получава се идеално кръгъл тръбен профил с еднаква дебелина по цялата дължина и точен външен диаметър. Гладкият, богат на смола, безшевен вътрешен слой, осигурява защита срещу отлагания и напластяване на котлен камък. В резултат е нужна по-малко енергия за транспортиране на питейната вода през тръбата.
Обикновено използваните тръби „GRP-CC” за питейно водоснабдяване в България са с SN10000, DN10, DN150-1100 mm, коефициентът на хидравлично съпротивление е 0,01 mm по Collebrook–White к. Те отговарят на изскванията на БДС EN 1796:2013.
Смолата на контактния слой с водата гарантира отлична устойчивост на абразия, като резултат на изключително еластичния и много гладък вътрешен слой, произведен по метода на центрофугално леене. В Германия при тестване за устойчивост е установено, че абразията е средно 0.2 mm след 100 000 цикъла. Следователно коефициентът на сигурност е надминат пет пъти с 1 mm дебелина на смолата, на вътрешния слой на центрофугално лятите тръби.
Съединяване на стъклопластови тръби GRP-CC
Най-често свързването на стъклопластовите тръби при монтаж е посредством муфи. За осигуряване на по-добра херметичност на съединението, муфите са с уплътнителни пръстени. Производителят на муфите трябва да е този, който е произвел и тръбите. Муфите трябва да са произведени от стъклопласт, съгласно БДС EN1796. Муфите трябва да са симетрични, с вътрешен уплътняващ слой от EPDM.
Свързването с муфи осигурява бързо и надеждно съединяване на тръбите и фасонните изделия-фланци, колена, тройници, кръстачи, редуцири. От друга страна, при съединяването на стъклопластови тръби с тръби и арматура от метал, се предпочита използването на фланцово съединение.
Полагане на стъклопластови тръби GRP-CC
Стъклопластовите тръби са по-леки в сравнение с много други предлагани тръби на пазара. Те се произвеждат със стандартна дължина от 6 m. Това улеснява полагането им на място. Много тесните и дълбоки изкопи не възпрепятстват техния професионален и бърз монтаж. Благодарение на тънките стени на тръбите разходите за тежка механизация за полагане могат да бъдат спестени. Малките диаметри дават възможност да се правят по-тесни траншеи, което води намаляване на разходите за изкопни работи. 16/11/2019 |