The IMER GROUP solutions were presented at SMOPYC 2008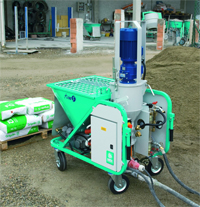 The IMER Group, based in Poggibonsi, Italy (leading European producer of machinery for the construction industry, machines and plants for the production, transport and application of concrete, spraying and conveying machines and specialist in earth moving machines) attended SMOPYC 2008 to showcase its top-level solutions, with the aim of strengthening its position on the Spanish market: the range of Mortar Spraying and Conveying Machinery and the new ORU LINK concrete mixing plant, particularly suited to the needs of the Spanish companies.
SMOPYC 2008 is of particular importance this year, given that the Italian group is pressing ahead with a strategy of strengthening its position on the Spanish-Portuguese market through its IMER Iberica branch, which recently opened new offices in Zaragoza.
SMOPYC 2008 was used by the IMER Group for the official Spanish launch of its Mortar Spraying and Conveying Division product range, to be distributed by IMER Iberica. The IMER range of spraying and conveying machines is very extensive (including mortar and plaster sprayers, transfer systems, screw pumps, continuous mixers and floor-screed conveyors) and was exposed at the company's stand at SMOPYC 2008. Also on show were some of the plaster sprayers from the Koine series (Koine 3 and Koine 5) and the multi-purpose Small 50 screw pump, which, thanks to their features and performance, have been a great success on the market.
The IMER Group's Koine 3 single-phase mortar and plaster sprayer for dry and pre-mixed materials, lightweight (191 kilograms) and compact (685 millimetres wide, 1450 long and 1270 high), combines high-level performance with contained power supply requirements. Designed for the mixing and spraying of pre-mixed materials in bags, it has a single-phase motor and a control panel with a three-speed inverter, giving material flow rates of 8, 11 and 15 litres per minute. The use of an “intelligent” inverter reduces the risk of clogging to a minimum. The Koine 3 is very easy to transport and works with a normal household meter, making it the ideal solution for renovation work. Like all the models in the Spraying and Conveying Line, it is made with high quality components, such as the stainless steel self-priming water pump and the diaphragm compressor, guaranteeing the reduction of maintenance to a minimum.
The Koine 5 plaster sprayer is the ideal solution for mixing and spraying pre-mixed materials in both bags and silos, such as lime/cement based plasters, plasters, gypsum and insulation plasters. This model, which has an S1 continuous duty motor (from 7.75 kW), is the perfect combination of high quality and contained cost. The water system, with a self-priming pump, guarantees high-performance pressure and flow rate and a long working life. Despite its large-capacity hopper (110 litres), the Koine 5 is small (680 millimetres wide, 1190 long and 1560 high), making it suitable for indoor work. The Koine range gives the customer the possibility of choosing the model best suited to their specific needs.
The IMER Group's Small 50 screw pump, one of the significant novelties, launched on the Spanish market, can spray a range of different materials, such as traditional plasters, pre-mixed materials, pre-mixed tixotropic products, waterproofing products, smoothing products and paint coatings. One of the new model's main strong points is that it is multipurpose and adaptable to a vast range of applications, thanks to a material flow rate of between 0.8 and 14 litres per minute.
The IMER Group's Concrete Machinery Division presented at SMOPYC 2008 its new ORU LINK plant. The system has been developed on the basis of a thorough analysis of the needs of some European (especially Spanish), Central and South American markets. It is available in a number of different versions and is intended for pre-mixed concrete materials, with a production rate of about 90-150 cubic metres an hour.
The new ORU LINK plant, distributed on the Spanish market by IMER Iberica, is very compact, thanks to the decision to install the cement batching unit above the aggregate transfer belt (thus taking up a minimum amount of space). It is designed to guarantee maximum material flow and, thus, maximum constancy of production. 26/05/2008 |