„Зелената” революция в бетона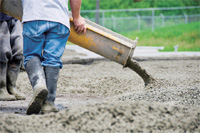 В съвременното строителство бетонът има широко приложение. Благодарение на безспорните си качества, той е предпочитан строителен материал за изпълнението не само на жилищни и обществени сгради, но и за пътни и хидротехнически съоръжения. Ежегодно производството му достига до 2 милиарда кубични метра, което далеч надхвърля производството на други промишлени продукти и строителни материали. Тук възниква въпросът доколко производството на неговата основна съставка – циментът, е екологично. Количеството на отделен въглероден диоксид, което съпровожда производствените процеси на портландцимента, е значително и поради тази причина се търсят алтернативни решения, които биха спомогнали за намаляването на въглеродния му отпечатък и за отговорното опазване на околната среда.
Производството на цимент включва термичната обработка на варовик и глина при температури в границите на 1400–1550°С, последвана от смилане на клинкера на фин прах, при което получаваме крайния продукт, познат като портландцимент. Близо 700kg въглероден диоксид се отделят в атмосферата за всеки тон произведен цимент. Ето защо, за да се намали въглеродния отпечатък, където е възможно, се редуцира количеството на цимент в бетонната смес, без да се компрометират якостта и дълготрайността на бетона. От една страна, в бетонната смес е заложено едно минимално количество на цимент, което досега не е разгледано в светлината на последните разработки в технологията на бетона. От друга – съществуват методи за включване на различни заместители на цимента, с които се запазват конструктивните качества на бетона.
Друг възможен подход е да се оптимизира бетонната смес, като в нея внимателно се интегрират компоненти, с цел да се извлече максимална полза от тях за бетона. Едно още по-радикално решение е употребата на различни видове полимери, за да се произведе бетон без съдържанието на цимент. При производството на този вид материали се отделят само 7% въглероден диоксид от количеството, което се отделя при производството на конвенционалния бетон.
Заместители на цимента
Заместители на цимента се използват повече от 2000 години. Първата документирана употреба е при строителството на амфитеатъра в гр.Помпей, където е добавена вулканична пепел от находището на вулканични туфи край гр.Поцули. Пуцолановите добавки, сами по себе си, дори и във фино смляно състояние, не свързват при реакция с вода, но при наличието на варовика от цимента, се образува отлично хидравлично свързващо вещество, благодарение на аморфния силициев диоксид. Той взаимодейства с калциевия хидроксид (портландит), получен по време на хидратацията на портландцимента, като при това се формират нискоосновни калциеви хидросиликати. С това се повишава плътността, химическата и корозионната устойчивост на циментовия камък и бетона. Освен вулканичните туфи в качеството на пуцоланови добавки се използват още трас, диатомит, вулканично стъкло и др. В сравнение с обикновения портландцимент, пуцолановият се характеризира с повишена водоплътност, химическа и корозионна устойчивост, по-ниска скорост на хидратация, по-ниска екзотермия (отделяне на топлина по време на хидратацията), по-голяма водопотребност и по-ниска мразоустойчивост. Пуцолановият портландцимент е особено подходящ за съоръжения, които се намират в контакт с вода или се намират постоянно под вода.
Смляната гранулирана доменна шлака е полу-пуцоланова добавка с широка употреба. Това се дължи на малкото количество калциев оксид, който съдържа, и затова е възможно частично да свърже при наличието на вода. Въпреки това, свързването и втвърдяването протичат с пълна сила при наличието на портландцимент.
Подмяната на 50 до 60% от количеството на портландцимента с шлака е често срещана практика. Шлакопортландциментът се използва при изпълнението на сгради и съоръжения, колкото и портландцимента. Заради намалената му екзотермия и повишена топлоустойчивост той е предпочитан пред портландцимента при изготвяне на бетони за масивни съоръжения, както и за конструкции в металургията и електрохимията, които оперират при постоянно повишени температури. Повишената му водо- и корозионна устойчивост го правят подходящ и за строителството на хидротехнически съоръжения. Ускореният процес на набиране на якост на шлакопортландцимента при термообработка позволява употребата му за изготвяне на бетонни и стоманобетонни изделия и конструкции в заводски условия.
Фино смлян варовик може да се добави към портландцимента като частичен заместител – до 20%. Качествата на получения цимент са сходни с тези на обикновения портландцимент. В допълнение към това се подобрява течливостта на бетона, както и се редуцира количеството топлина, което се отделя при хидратацията. Добавката от варовик може да се сложи и отделно към цимента, но когато варовикът на прах се смеси с циментовия клинкер в заводски условия, се получава много по-стабилен продукт.
Пепелният портландцимент също намира своето широко приложение съдържа като активна минерална добавка летяща пепел от електрофилтрите на ТЕЦ-овете. Според нормите в България могат да се използват силициеви (кисели) пепели и варосъдържащи (основни) пепели. Този вид портландцимент съдържа активна минерална добавка в количество 20–35%. Пепелните портландцименти са подходящи за изпълнението на сгради и съоръжения, които са в контакт с вода и влага, за бетониране на масивни конструктивни елементи, като язовирни стени, фундаменти и др., поради по-малката им екзотермия, а така също и за конструкции, изложени на действието на агресивни среди. Не са подходящи за изпълнение на бетонови работи в зимни условия, както и за хидротехнически бетони с повишени изисквания за мразоустойчивост.
Друг, малко нетрадиционен, но добър частичен заместител на цимента е пепелта от оризови люспи, която е остатъчен продукт от оризовата промишленост. Тайланд е сред големи производители и през 70-те години на ХХ век са направени редица проучвания върху контролираното изгаряне на оризови люспи с цел да се получи един консистентен продукт. Люспите се изгарят в пещи, подобни на въртящите се пещи за цимент. При този метод не се получава добър краен продукт, тъй като частичното изгаряне в ограничено пространство води до отклонения в качеството. Оризовите люспи в не изгорялата си форма също могат да бъдат смлени и използвани като заместител. Те имат сложни форми и работят най-добре, когато са смесени с клинкера, с цел да се редуцира количеството вода в бетонната смес.
Метакаолинът е отпадъчен продукт в керамичната индустрия. Образува се при калцинирането на каолинова глина при температури от 650 до 850ºС, след което се обработва до постигането на степен на смилане от порядъка на 700 до 900m2/kg. Полученият материал има качества като пуцоланите. Може да се добави към бетонната смес и под формата на немодифицирана глина, което прави бетона по-„зелен”. Въпреки това, сравнително високата цена на метакаолина го възпрепятства от широка употреба в строителството.
Естествените пуцолани като вулканичната пепел и пемза се използват, когато има местни производители на тези материали. Транспортирането на дълги разстояния оставя голям въглероден отпечатък и следователно е неизгодно от екологична гледна точка.
Полимербетон
Интересно нововъведение е използването на полимери. Те могат да се комбинират с доменна шлака, летящи пепели и естествени пуцолани, за да се произведе бетон без съдържанието на цимент. Полимербетонът представлява втвърден бетон, пропит с полимерни или мономерни състави, които се полимеризират в бетона, и има широко приложение като подходящ заместител на традиционния бетон. В сравнение с него, този вид бетон има редица предимства като подобрени характеристики, по-голяма химическа устойчивост и по-ниска водопотребност. Най-често срещаните пълнители за полимербетон са фракции от кварц, варовик, пясъчник и доломит. Други подходящи пълнители са шисти, каолин, талк и слюда. Възможно е якостта на натиск на такива бетони да достигне 60MPa според заложените в проекта характеристики на бетона. Якостта на опън е в границите от 10 до 15% от якостта на натиск. Характерно е и ограничено съсъхване – коефициентът на линейно разширение е от порядъка на 5.10-6ºС.
Друго основно предимство на полимербетоните е повишената пожароустойчивост в сравнение с традиционните бетони от портландцимент. Обикновеният бетон започва да губи якостните си характеристики, когато температурата достигне 400ºС, а при 650ºС вече е напълно компрометиран. Някои видове полимербетони могат да запазят качествата си при температури от 1000ºС, при това с минимални загуби на якост. Тази повишена пожароустойчивост е голям плюс особено при сгради и съоръжения със завишени изисквания спрямо пожарната безопасност. И не на последно място, при производството на полимербетоните се отделят едва 7% въглероден диоксид от количеството, което се отделя при производството на портландцимента.
Оптимизиране на бетонната смес
В продължение на години традиционните съставки на бетона включват цимент, вода, чакъл и пясък в определени пропорции в зависимост от специфичните изисквания, заложени в дадения проект. Строителството на все по-мащабните и пълни с предизвикателства сгради и съоръжения обаче е предпоставка за разработването и внедряването на различни видове добавки, които подобряват свойствата на бетона и улесняват в голяма степен строителните процеси. Разбира се, количеството им в бетонна смес е ограничено – до 5% от масата на цимента. В противен случай, може да влоши качеството на бетона. С употребата на добавки се подобрява обработваемостта на сместа, намалява се разслояването, подобрява се възможността за изпомпване и регулиране на сроковете на свързване – ускоряване или забавяне. Също така могат да се постигнат намаляване на съсъхването, ускоряване набирането на якост, както и намаляване на водопропускливостта. Добавки могат да се използват и с цел пенообразуване и въздуховъвличане.
Самоуплътняващ се бетон
На пръв поглед, самоуплътняващият се бетон може да не изглежда много екологичен, тъй като количеството на цимент при него е завишено. Въпреки това, той печели зелени точки, защото се спестяват време и енергия. На първо място, значително могат да бъдат подобрени условията на труд на работната площадката. Отпада нуждата от вибратори, спестяват се трудоемките операции по уплътняването на бетонната смес – намаляват се разходите по заплащане на труда и се увеличава производителността. Самоуплътняващият се бетон е силно пластична смес, която не се разслоява и безпроблемно запълва кофражните форми. Уплътнява се под действие на собствената си тежест и е идеално решение при елементи с висока степен на армиране, при които полагането на обикновен бетон предполага въвличане на много въздух и компрометиране на физичните и механичните свойства. Сред най-важните му качества са пластичността и стабилността. Голямата пластичност се дължи на използваните добавките, които от своя страна намаляват количеството на необходимата вода.
Основните предимства на самоуплътняващия се бетон са свързани с подобрено качество на бетонната смес – свойствата на вече втвърдения бетон са сходни с тези на конвенционалния бетон. Той има по-малък вискозитет и поради тази причина скоростта му на изпомпване е по-голяма. Това, от своя страна, води до по-ниско налягане в бетонпомпата и по-бавно износване на нейните компоненти. Така се постига и по-бързо полагане на сместа в кофражните форми, следователно и по-бързо строителство. Създават се идеално гладки бетонни повърхности за разлика от обикновения бетон, при който по готовите декофрирани елементи могат да се забележат редица несъвършенства, причина за които е останалият в сместа въздух. Осигурява се и по-добра устойчивост на външни въздействия и дълготрайност, заради по-плътната структура. Това намалява значително разходите за поддръжка и поправки по време на експлоатационния период на една сграда. 10/12/2011 |